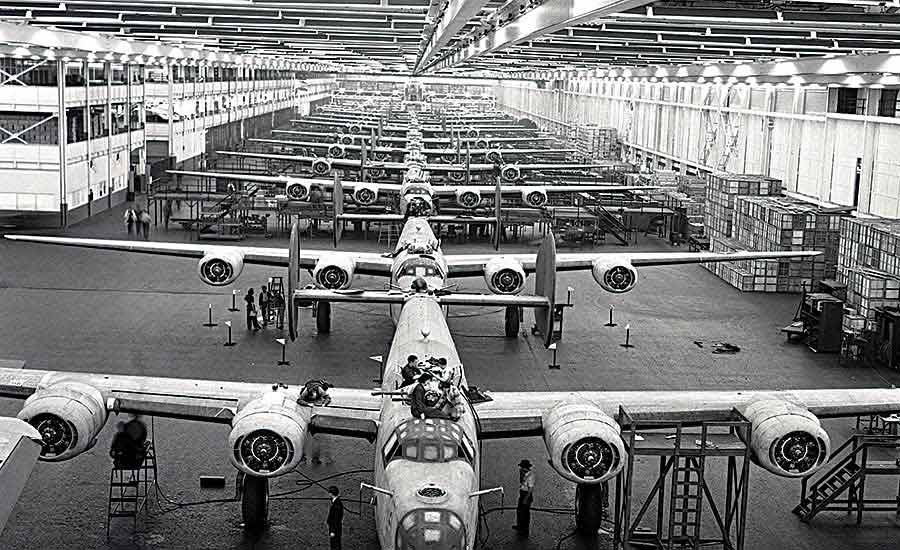
Amidst the backdrop of World War II and Henry Ford’s complex political views regarding the US involvement, a pivotal moment in production operations history took place as Ford Motor Company embarked on an extraordinary endeavor. This story revolves around the transformation of Willow Run, also known as Air Force Plant 31, from a bomber-a-day plant to a groundbreaking bomber-an-hour plant. Set in the heart of the war effort, Ford’s decision to take over this plant and revolutionize its production operations left an indelible mark on industrial history.
Henry Ford’s Political Views and the Decision to Take Over Willow Run:
Henry Ford, the iconic founder of Ford Motor Company, held complex political views regarding the United States’ involvement in World War II. Initially, he was hesitant to support the war effort and had publicly voiced his opposition to military intervention. However, as the war intensified, Ford realized the crucial role that industrial production would play in supporting the nation’s defense and the war effort.
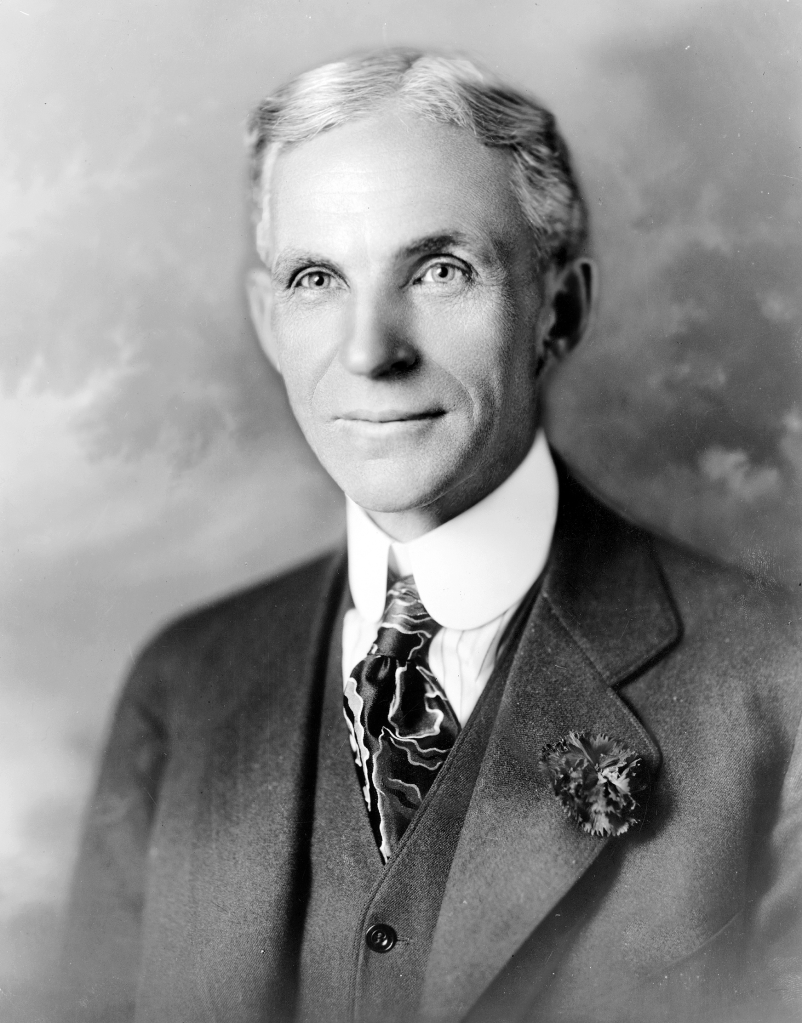
Consequently, Ford accepted the idea to take over Willow Run, a massive production facility previously managed by the federal government, to contribute significantly to the war effort. The plant had been tasked with manufacturing B-24 Liberator bombers, essential for air support during the war. Understanding the vital importance of the task at hand, Ford’s decision reflected a shift in focus towards prioritizing production operations that would make a substantial impact on the war front.
The Transformation: From Bomber-a-Day to Bomber-an-Hour
When Ford Motor Company took control of Willow Run, they faced an extraordinary challenge – accelerating bomber production exponentially. The original production rate of one bomber per day would not suffice to meet the demands of the war effort. Ford’s goal was ambitious: to produce a staggering one bomber every hour.
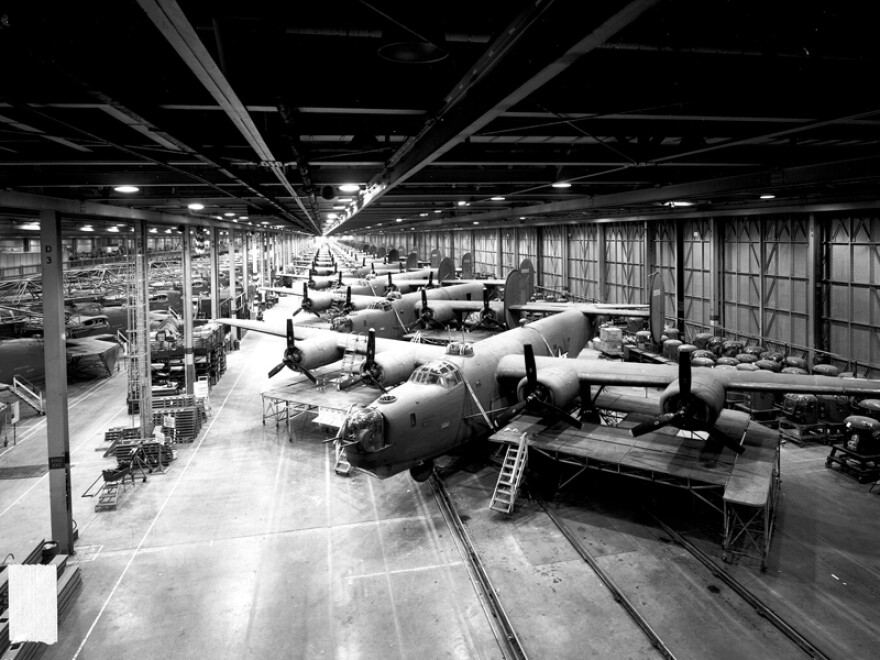
Ford’s engineering prowess and expertise in mass production played a pivotal role in the transformation of the plant. Embracing mass production principles, they implemented highly efficient production techniques to streamline processes. Assembly lines were optimized and significantly increasing efficiency.
The Power of Collaboration:
Beyond leveraging Ford’s engineering ingenuity, the success of Willow Run’s transformation was fueled by effective collaboration among teams. Skilled workers, engineers, and managers worked harmoniously, recognizing the urgency and magnitude of their mission. This sense of unity and collective purpose became the driving force behind the rapid expansion of production capabilities.
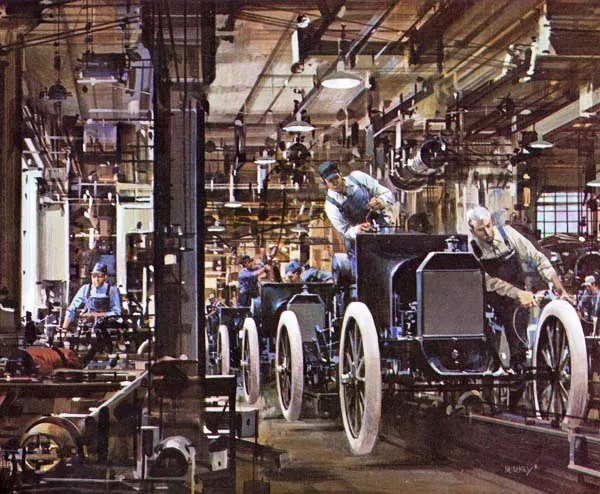
Implementing Mass Production at Willow Run
Drawing from its successful experience with mass production at its car manufacturing facilities, Ford Motor Company applied the same principles and practices to streamline operations at Willow Run. The goal was to optimize efficiency, increase output, and achieve the ambitious target of producing a bomber every hour.
- Assembly Line Efficiency: Ford’s expertise in creating efficient assembly lines played a crucial role in the transformation of Willow Run. They meticulously planned the layout of the production floor, ensuring a seamless flow of materials and components. Each worker was assigned a specific task in the assembly process, minimizing downtime and maximizing productivity.
- Standardization and Simplification: To expedite production, Ford standardized parts and processes wherever possible. This approach simplified the manufacturing process, reduced the need for specialized training, and facilitated faster assembly. Additionally, common components across different models of bombers enabled interchangeable parts, further streamlining production.
- Training and Skill Development: Ford invested heavily in training its workforce at Willow Run to ensure everyone was well-versed in mass production techniques. They drew on their experience in training automotive workers to quickly adapt to the high demands of aircraft manufacturing. This upskilling of the workforce played a significant role in achieving the desired production rates.
- Continuous Improvement: The principle of continuous improvement, central to Ford’s mass production philosophy, was instilled at Willow Run. Workers and managers were encouraged to identify inefficiencies and suggest innovative solutions to enhance productivity continually.
- Scale and Resource Allocation: Ford allocated substantial resources to Willow Run, including skilled manpower, machinery, and engineering expertise. This commitment allowed the plant to operate at full capacity and meet the demands of the war effort.
Ford Motor Company’s successful transformation of Willow Run into a bomber-an-hour plant was a testament to its visionary leadership, innovative practices, and unwavering commitment to mass production techniques. Drawing on its expertise in the automotive industry, Ford applied mass production principles, standardized processes, and optimized assembly line efficiency to achieve unprecedented levels of productivity.
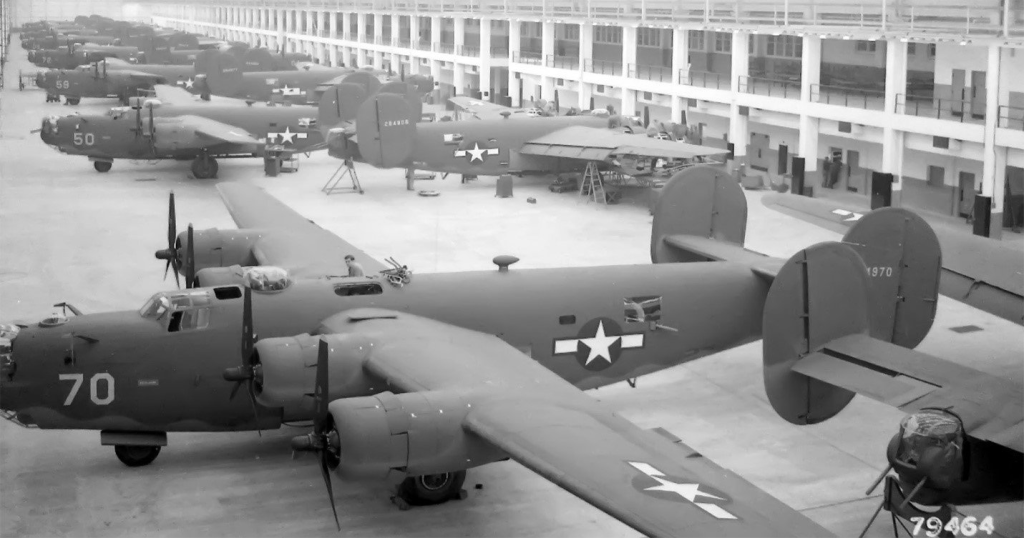
The efforts at Willow Run exemplify the remarkable contributions made by the manufacturing sector during World War II. Ford’s dedication to excellence not only bolstered the war effort but also left a lasting impact on production operations. The lessons learned from this extraordinary achievement continue to shape modern manufacturing practices and inspire industries worldwide.
I