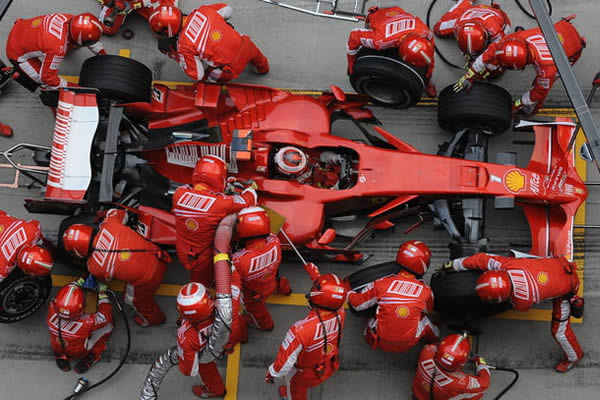
In the ever-evolving world of manufacturing and beyond, time is a precious resource that can make or break a business’s success. To meet the demands of fast-paced markets and changing consumer needs, organizations sought ways to reduce downtime, increase flexibility, and enhance productivity. This quest for efficiency led to the development of a groundbreaking method known as Single Minute Exchange of Die (SMED). In this blog post, we will explore the origins of SMED, its significance in manufacturing, and its versatile applications in various industries beyond the factory floor.
- The Founding of SMED:
SMED was pioneered by Shigeo Shingo, a renowned Japanese industrial engineer and a key figure in the development of the Toyota Production System (TPS). In the 1950s and 1960s, Shingo observed that excessive time was wasted during machine changeovers in manufacturing processes. Traditional changeover methods resulted in lengthy downtime, hindering the ability to produce different products quickly.
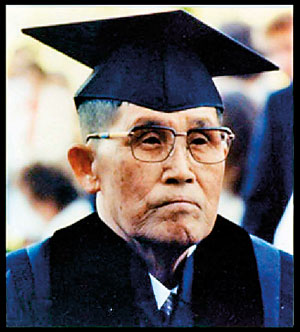
Shingo’s innovative approach to tackling this problem involved identifying and separating external setup tasks (those that can be performed while the machine is running) from internal setup tasks (those that require the machine to be stopped). By converting as many internal setup tasks to external ones, the time required for changeovers could be drastically reduced.
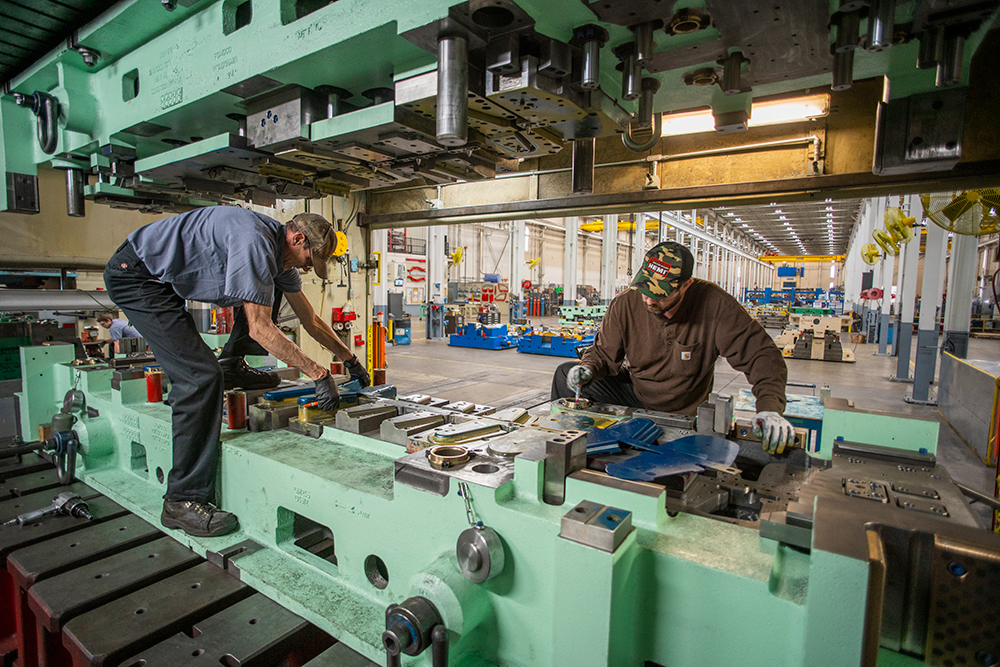
- The Why Behind SMED:
The primary goal of SMED was to achieve rapid changeovers, reducing setup times to less than ten minutes or even a single minute, hence the name “Single Minute Exchange of Die.” By doing so, manufacturers could minimize production disruptions, accommodate smaller batch sizes, and enhance production flexibility. This not only reduced inventory costs but also enabled businesses to respond swiftly to customer demands and market changes.
- The Global Influence of SMED:
The success of SMED in the Toyota Production System quickly caught the attention of the manufacturing world. As Japan’s manufacturing prowess gained international recognition, other companies sought to learn from their methodologies. Today, SMED is a fundamental Lean Manufacturing technique and has been widely adopted by manufacturers worldwide.
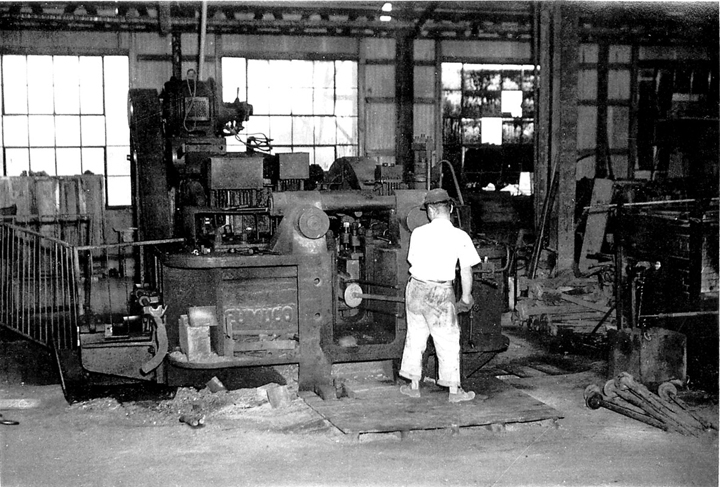

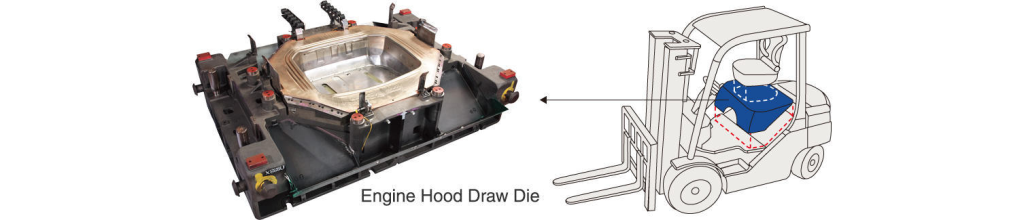
SMED’s influence extended beyond the factory walls and was incorporated into various Continuous Improvement methodologies such as Total Productive Maintenance (TPM) and Lean Six Sigma. By implementing SMED principles, organizations have transformed their operations, achieving higher efficiency, reduced waste, and improved overall competitiveness.
- Adapting SMED beyond Manufacturing:
While SMED originated in manufacturing, its principles have proven adaptable to diverse industries and processes:
a. Healthcare: In hospitals and healthcare settings, SMED principles have been applied to streamline patient room setups, surgical procedures, and equipment changeovers, leading to faster patient care and improved resource utilization.
b. Service Industries: SMED concepts have been implemented in service industries, such as restaurants, to optimize table turnovers, reducing waiting times and improving customer satisfaction.
c. Software Development: In software development, SMED-inspired practices have been utilized to minimize the time required for code deployments, making the process more efficient and reliable.
d. Transportation: In logistics and transportation, SMED principles have been used to optimize loading and unloading processes, reducing downtime and enhancing delivery speed.
The revolutionary concept of Single Minute Exchange of Die (SMED) introduced by Shigeo Shingo has transformed the manufacturing landscape and reverberated across industries worldwide. By emphasizing rapid changeovers and reducing downtime, SMED has unlocked new levels of efficiency, flexibility, and responsiveness in manufacturing processes.
SMED’s far-reaching influence extends beyond manufacturing and has been successfully adapted in diverse fields, including healthcare, service industries, software development, and transportation. As businesses continue to seek ways to enhance productivity and optimize their processes, the timeless principles of SMED remain a beacon of efficiency, guiding organizations towards a more streamlined and competitive future.
Leave a comment