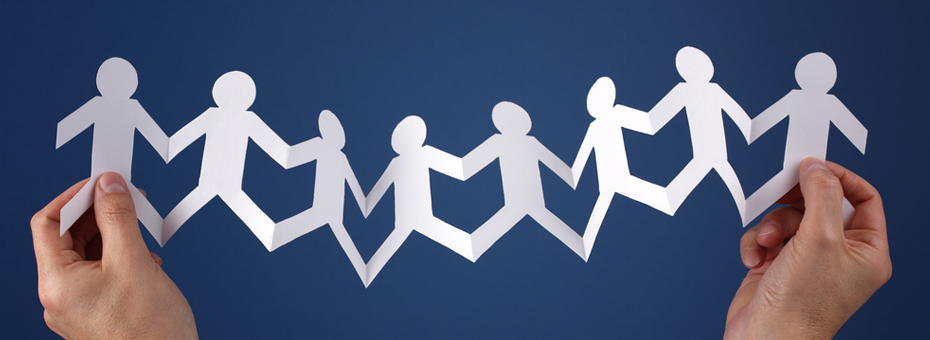
The principles of lean management can be applied to the HR department, leading to more efficient and effective processes and practices. While lean management is often associated with manufacturing and production environments, its core principles can be adapted to various areas, including HR.
Here are some ways in which lean management philosophy can be applied in the HR department:
- Eliminating waste: Lean management aims to eliminate waste in all forms, including unnecessary steps, duplication of efforts, and inefficient processes. In the HR department, this can involve streamlining recruitment and onboarding processes, reducing paperwork, and automating routine administrative tasks to free up time for more value-added activities.
- Continuous improvement: Lean management emphasizes the concept of continuous improvement, encouraging teams to regularly review and enhance their processes. In the HR context, this could involve collecting feedback from employees on HR services, identifying areas for improvement, and implementing changes to enhance the employee experience and optimize HR operations.
- Standardized processes: Standardizing processes helps ensure consistency and efficiency. HR departments can establish standardized procedures for activities such as performance evaluations, training and development programs, and employee onboarding. This enables smoother operations, reduces errors, and allows for better measurement and analysis of HR metrics.
- Value stream mapping: Value stream mapping is a lean tool used to analyze and improve the flow of activities in a process. Applying this tool to HR processes can help identify bottlenecks, non-value-added steps, and areas of improvement. By mapping the end-to-end HR process and visualizing the flow of activities, the department can identify opportunities for streamlining and enhancing efficiency.
- Employee empowerment and engagement: Lean management encourages employee involvement and empowerment. In the HR context, this can involve promoting employee participation in process improvement initiatives, seeking input on HR policies and programs, and fostering a culture of open communication and collaboration.
By adopting lean management principles, the HR department can drive greater efficiency, improve the employee experience, and align HR practices with the overall goals and objectives of the organization.
References:
- Liker, J. K., & Meier, D. (2007). The Toyota Way Fieldbook. McGraw-Hill.
- Womack, J. P., Jones, D. T., & Roos, D. (1990). The Machine That Changed the World. Rawson Associates.
- Sanders, M. (2013). The Lean HR Handbook: A Guide to Creating a Sustainable Lean Transformation in HR. Productivity Press.